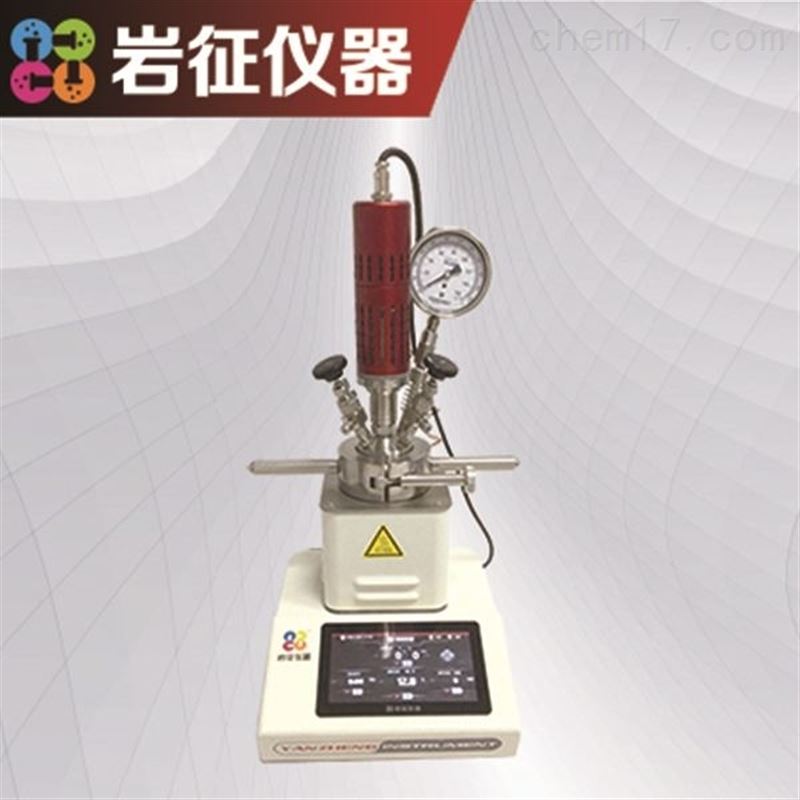
在化工、医药等领域,酯化反应是一种常见的有机合成反应,广泛应用于各类产品的生产过程中。酯化反应釜作为实现这一过程的关键设备,具有重要地位。本文将详细介绍结构、工作原理、性能评价以及改进策略和发展前景等方面。
一、结构与原理
酯化反应釜主要由反应釜主体、搅拌装置、加热/冷却系统、安全装置等组成。反应釜主体通常采用不锈钢或搪瓷等耐腐蚀材料制造,以适应各种腐蚀性化学品的反应条件。搅拌装置则采用机械搅拌或磁力搅拌等方式,以保证反应物料的充分混合和分散。加热/冷却系统用于控制反应温度,保证反应的顺利进行。安全装置则包括紧急排放阀、压力表、温度计等,以确保反应过程的安全性。
酯化反应釜的工作原理是基于酸和醇在催化剂的作用下发生酯化反应,生成酯类化合物。该反应通常需要加热、搅拌和催化剂等条件,以保证反应的效率和产物的质量。
二、性能评价
评价性能主要从以下几个方面进行:
1. 反应效率:反应效率是评价反应釜性能的重要指标,通常以单位时间内反应物的转化率来衡量。高反应效率可以提高生产效率和降低能源消耗。
2. 反应条件:反应条件包括温度、压力、搅拌速率等,这些因素直接影响着反应的速率和产物的质量。优化反应条件可以提高产物的质量和收率。
3. 副反应:副反应是指在酯化反应过程中产生的其他化合物,如水、醇等。降低副反应的发生可以减少能源消耗和降低分离成本。
4. 设备材质与结构:设备的材质和结构直接关系到其耐腐蚀性、稳定性和使用寿命。选择合适的材质和结构可以降低设备维护和更新的成本。
5. 操作便捷性:设备的操作便捷性也是评价其性能的重要因素,包括设备的安装、调试、操作和维护等方面。简单的操作可以提高工作效率并降低人工成本。
三、改进策略
针对反应釜存在的问题,以下几种改进策略值得关注:
1. 结构改进:优化搅拌装置的设计可以提高物料的混合效果,降低死角,提高反应效率。同时,改进加热/冷却系统的结构可以更好地控制反应温度,提高产品的质量和收率。
2. 工艺改进:采用新型的催化剂和优化反应条件可以降低副反应的发生,提高产品的纯度和收率。同时,采用连续化生产工艺可以提高生产效率,降低能源消耗和人工成本。
3. 设备改进:采用新型耐腐蚀材料和表面处理技术可以提高设备的耐腐蚀性能和使用寿命。同时,引入自动化和智能化的控制系统可以提高设备的操作便捷性和安全性。
四、发展前景
随着科技的不断发展,酯化反应釜将朝着高效化、安全化、环保化和智能化方向发展。未来将采用更先进的搅拌技术、加热/冷却系统和安全装置,以提高反应效率和产品的质量。同时,随着绿色化学的兴起,环保型的酯化反应釜将成为未来的发展趋势。此外,随着工业4.0的发展,智能化将成为未来的重要发展方向,实现自动化、远程监控和预测性维护等功能。
总之,酯化反应釜作为化工、医药等领域的重要设备,其性能的优劣直接影响到产品的质量和生产效率。随着科技的不断进步和市场需求的不断变化,性能将不断提升,应用领域也将更加广泛。